Vacuum assisted Resin Transfer Moulding



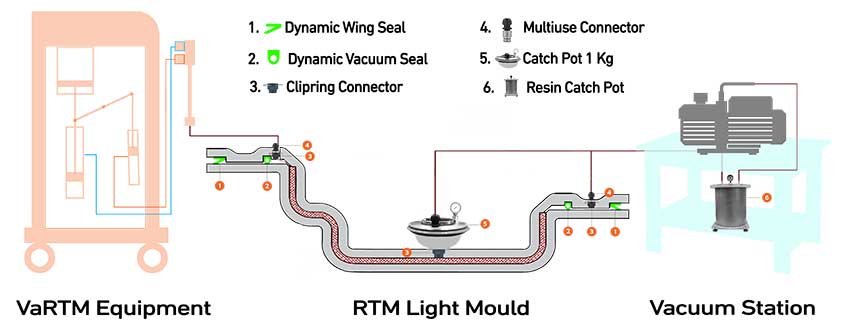
Vacuum assisted Resin Transfer Moulding is a closed-mould manufacturing solution. Composite parts are made with polyester or vinyl ester resin system and reinforcements like fibreglass or carbon fibres. Our VaRTM equipment is perfect choice for traditional Light RTM, Silicone Bag Infusion or Bagging processes.
These are designed for low pressure injection of resin into the mould / bag. Catalyst pump works on positive feed system allowing to adjust catalyst to resin ratio. Solvent flushing and air purge ensures quick and easy cleaning.
Recirculation Individual / Complete (RIC)
Unmixed resin and catalyst to cycle from dispense head back to reservoir. Unique feature is that either of the two liquids can be recirculated individually without mixing. This allows material lines to remain de-gassed without wastage. Constant movement of material prevents settling of fillers.
Mould Back Pressure Control (MBP)
Solvent & Air Purge
Immediate cleaning and drying of dispense head is easily operated via SAP controls mounted on the user panel. Independent solvent flush prevents curing of resin within the mix and dispense head. Separate air flush and drier ensures quick and efficient cleaning.
Positive Feed Slave Pump
Catalyst pump works as a slave with resin pump. Catalyst-to-resin percentage can be adjusted quickly without any tool. Percentage can be varied between 0.5% to 3.5%.
Cabinet-n-Cart
Compact design and robust build quality of the structure ensures long life. Specially formulated surface coatings to withstand aggressive nature of catalyst and resin.
Data Programming
Upto 50 injection settings can be per-programmed. Real time data logging, storage & transfer can be done in few easy steps.
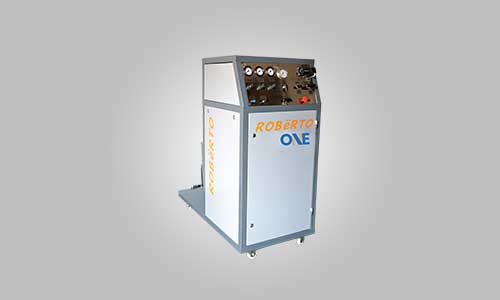
Applications
• Marine and Watercraft
• Pools and Waterslides
• Automotive Parts
• Railway Interiors
• Windmill Parts
• Industrial Products
Models -> |
|
|
|
Specifications |
User friendly operation and low maintenance. Suitable for all forms of closed moulding processes. |
Semi-automated operation and easy maintenance. Ideal for multiple moulds and high volume production. |
Touch Screen operation, programable system for advanced user interface. Simply high-volume production with multiple moulds. |
Resin Compatibility |
Polyester / Vinyl Ester |
Polyester / Vinyl Ester |
Polyester / Vinyl Ester |
Air Requirement |
100 psi / 7 bar @ 15 cfm |
100 psi / 7 bar @ 15 cfm |
100 psi / 7 bar @ 15 cfm |
Resin Output |
± 2 kg / min |
± 2 kg / min |
± 2 kg / min |
Output / Stroke |
180 cc |
180 cc |
180 cc |
Resin Pump |
11:01 |
11:01 |
11:01 |
Catalyst Ratio |
0.5 % - 3.5 % |
0.5 % - 3.5 % |
0.5 % - 3.5 % |
Recirculation Independent / Complete |
Independent & Complete |
Complete |
Complete |
Adjustable Independent Solvent Flush |
● |
● |
● |
Independent Air Flush & Dry Toggle |
● |
● |
● |
Roberto Dispense Head w/ Static Mixer |
● |
● |
● |
Stroke Counter |
● |
● |
● |
MBP Controller |
● |
● |
● |
Panel Control |
Ball Valves |
Push Buttons |
Touch Screen |
PLC Touch Screen |
● |
||
Programmable Injection Settings |
● |
||
Data Logging & Transfer |
● |
||
Password Protect |
● |
||
Body Type |
Cabinet-n-Cart |
Cabinet-n-Cart |
Cabinet-n-Cart |